Analyse, understand and anticipate the failure of a component or piece of mechanical equipment to be able to judge its integrity.
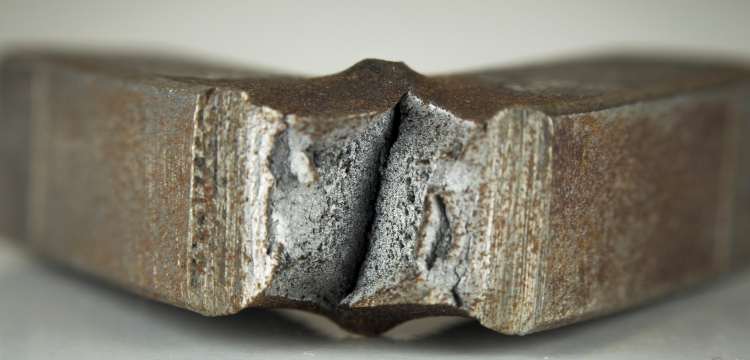
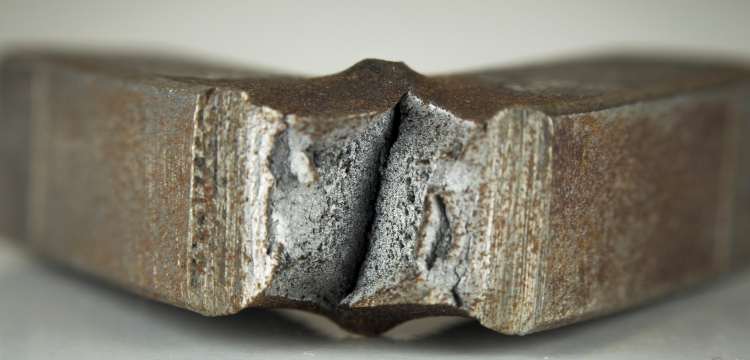
Fracture mechanics
Your expectations
Following the cracking, breakage or deformation (impact or stress) of a component or piece of equipment, you want to carry out an analysis to :
- Identify the causes and origin of the cracking (material, design, use, etc.),
- Understand the degradation phenomenon(s),
- Assess the criticality of the defect and the associated risk,
- Assess whether the risk is present in the rest of a population of similar components (batch, group, assembly, etc.).
- Define a safeguard strategy (repair, replacement, maintenance, checks, surveillance, monitoring, etc.)
- Identify remedies to prevent recurrence.
Our solutions
The presence of cracks in a structure can considerably reduce its strength and reliability, even leading to failure.
We offer support that can start with the identification of a crack or defect in a structure and end with the determination of its criticality.
We can also analyse the material after a failure to gauge its role in the damage and assess the level and characteristics of the stresses seen in service.
Apart from determining the cause of the failure, this data provides input for a problem-solving or monitoring approach that can be based on fracture mechanics (harmfulness of the defect, residual service life, etc.).
Detecting, analysing, assessing the harmfulness and finally the propagation of a crack enables the strength of a structure to be controlled.
Predictive analytical and numerical calculation tools can be used to assess crack initiation and propagation under fatigue or static loads. They cover a large number of configurations, from the simplest to the most complex (multiaxial stresses, crack orientation), and provide decision support.
The detection, analysis, assessment of the harmfulness and finally the propagation of a crack enable the strength of a structure to be controlled.
Predictive analytical and numerical calculation tools can be used to assess crack initiation and propagation under fatigue stresses in service.
They cover a large number of configurations, from the simplest to the most complex cases (multiaxial stresses, crack orientation) and provide decision-making assistance.
Cetim's experts propose and carry out a structured and factual approach based on well-known standards (BS 7910, RSE-M, API 579, etc.) or using innovative methods based on 3D digital representation:
- Failure analysis, taking into account the history, operating conditions and environment of the component and machine, as well as coupling with our multi-trade experience,
- Qualitative and/or quantitative characterisation of the failure mode, the stresses under which the cracking occurred, the role of the material in the damage (presence of a defect, non-conformity, etc.).
- Implementation of a test plan to identify the mechanisms (propagation thresholds and speed, material toughness, behaviour law, etc.),
- 3D and analytical calculations,
- Use of simulation tools to confirm damage hypotheses,
- Advice and support for failure resolution and redesign.
Your benefits
Cetim, independent and neutral technical centre, is specialised in the mechanical behaviour of structures and equipment during operation.
Enriched by its experience of over 50 years, our experts deal with nearly 1,500 new cases every year, in all fields of mechanics: mechanical, metallic, plastic and composite damage, etc. on various equipment or components.
A team dedicated to fracture mechanics, supported by specialists in failure analysis and simulation.
A comprehensive, multi-skilled approach that deals with failures from their origins right through to the implementation of practical solutions.
Our organisation is recognised by legal experts and insurance companies.
Neutrality and independence, guaranteeing you the objectivity of our results.
Support via Cetim Academy® customised training courses, with Qualiopi certification.