Calculation and simulation to improve the performance and robustness of your products, reduce the time-to-market and maximize equipment availability.
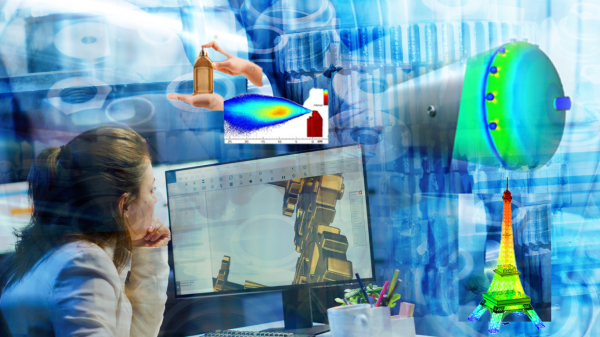
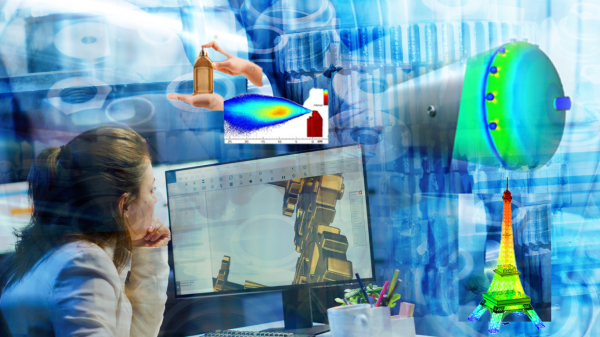
Digital engineering: calculation and simulation
Your expectations
As part of your product development, you are looking to improve the performance and robustness of your products (design to cost, “getting it right the first time”), accelerate the validation of your products and reduce the time to market (reducing testing time and costs)
You want to guarantee your customers that you will provide in-service operational maintenance for your products for maximum availability rate.
In more concrete terms, you need to:
- Validate the mechanical sizing of a new product or a new design of metallic or composite parts to the exact specifications required
- Make a technological leap by integrating numerical simulation tools, to provide services with more added value
- Estimate the Remaining Useful Life (RUL) of your components or items of equipment with a view to providing optimum through-life support
- Broaden your current computation skills or integrate new ones to offer new simulation / computation services within your engineering and design department
- Improve the reliability of your projects through calculation-test correlations
- Validate and optimise your manufacturing processes (cutting & deep drawing, forging, etc.)
Our solutions
As a key player of the Industry 4.0 with expertise in numerical simulation and mechanical engineering, we offer you computation & simulation services and assistance perfectly suited to your trade requirements.
Our experts will also help your teams upgrade their skills by providing dedicated training courses.
Below is a list of our areas of expertise:
- Numerical simulation and design of pressure equipment in compliance with applicable regulations (CODAP, COVAP, CODRES, EN 13445, etc.)
- Seismic simulation
- Computational Fluid Dynamics (CFD) simulation
- Structural mechanics simulation
- Simulation of fluid / structure interactions
- Thermo-mechanical simulation
- Simulation of manufacturing processes
- Simulation of bolted, welded, riveted and bonded joints
- Fatigue strength simulation on metallic or composite materials
- Simulation of cathodic corrosion protection systems
- Simulation of mechanical components in power transmission systems (toothed wheels, reduction gears, shafts, etc.)
- Simulation of multi-material sealing solutions
- Topology optimisation for parts made by additive manufacturing
- Optimisation of the design of composite parts
- Modelling of non-destructive tests
ZOOM ON HYDROGEN
HyMEET, our technological platform dedicated to H2, provides mechanical engineering with resources and skills needed to master low-carbon hydrogen production, distribution, storage and utilization technologies. HyMEET combines an ambitious R&D program with a €25 million investment in resources dedicated to characterization and validation tests (up to 1000 bar and in a range of temperatures from deep cryogenics to high temperatures) as well as consulting and training.
Its activities are dedicated to:
- Characterizing the behavior of materials in contact with hydrogen
- Development of specific test methods
- Characterization of specific mechanical equipment and systems in severe hydrogen environments.
Our equipment enables:
- Mechanical characterization of materials using fatigue machines in a high-pressure hydrogen environment
- Control of sealing systems and plant containment, with test benches developed to study gas diffusion phenomena, resistance to rapid decompression and sealing performance under severe conditions
- The study of the ageing of test specimens in high-pressure autoclaves
- Tests under cryogenic conditions for the use of hydrogen in liquid form, with several cryostats fed by a helium-hydrogen liquefier
- Multiphysics tests with pressure, temperature and .... cycling.
- Manufacture of thermoplastic composite parts (tanks, tubes) by in-situ deposition and consolidation (in real time, with no further steps required) using our HySPIDE TP robotized cell.
Your benefits
- The guaranteed impartiality of a Technical Centre
- Multi-sector and multiphysics expertise for a robust and comprehensive assistance service
- An organisation that will offer you agile and competitive services
- Guaranteed compliance with the applicable regulatory requirements through our active contribution to the various standardisation bodies
- A head start in the Industry 4.0 with access to the latest simulation methods and technologies
- A dedicated range of Cetim Academy® trainings (classroom and online courses)